A simple hydrophone
Here's a blast from my past: a piezo-electric hydrophone. This was
my very first research gadget that I ever built. I put it together
roughly 10 years ago for my senior research project during either my 2nd
or 3rd senior year of undergrad.
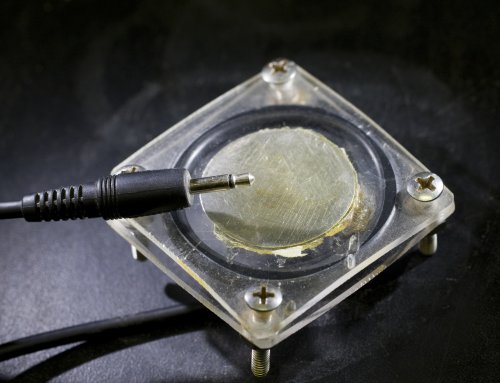
The goal was to listen to predatory whelks feeding on mussels in order to estimate handling time. Because you can't really see the business end (the radula) of a whelk when it's feeding, the only good way to determine when a whelk is drilling is to listen for it.
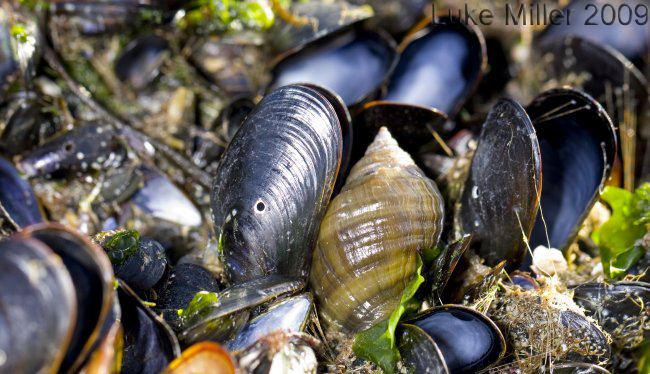
Note the drill holes in the Mytilus edulis shells around the Nucella lapillus shown above.
The hydrophone is based on a piezoelectric noisemaker, commonly found in things like home smoke detectors and Hannah Montana singing greeting cards (Note: it turns out that Hannah Montana greeting cards don't actually contain piezo discs. Stick with smoke detectors).
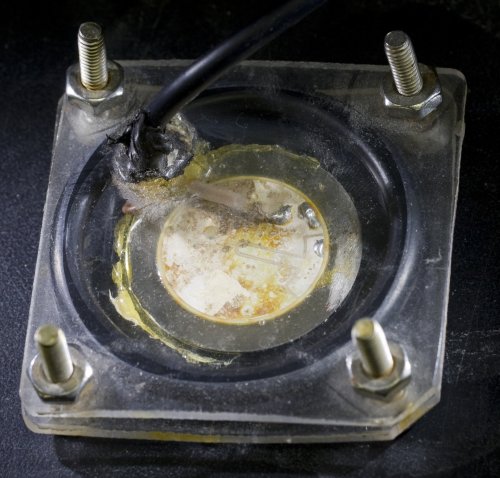
When I was actually recording whelks drilling, I found that it helped
to use some 2-ton epoxy to glue one of the valves of the mussel directly
to the outer face of the plexiglass, right on top of the piezo unit. When
a whelk started drilling the mussel, this transmitted the drilling
noise(more of a scraping noise really) directly to the hydrophone,
helping itstand out from the background noise of water moving through
the seawater system. This same system could be glued to a rock to listen
to the grazing sounds of herbivorous gastropods. Just don't do anything
lame like listen to whale songs. Study something interesting that
doesn't have a backbone!
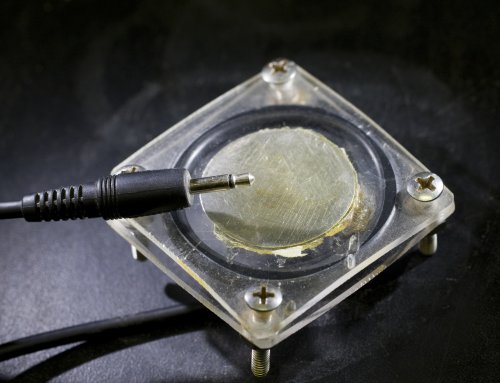
The goal was to listen to predatory whelks feeding on mussels in order to estimate handling time. Because you can't really see the business end (the radula) of a whelk when it's feeding, the only good way to determine when a whelk is drilling is to listen for it.
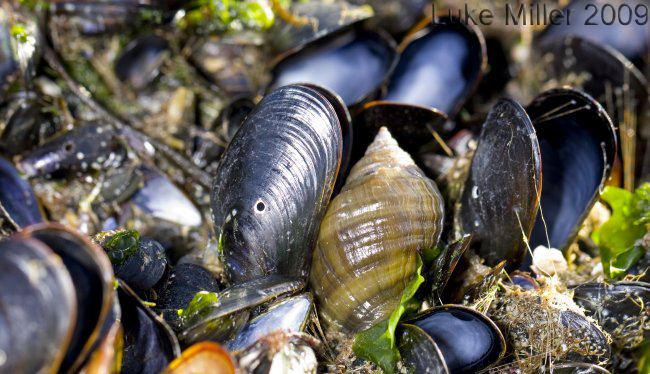
Note the drill holes in the Mytilus edulis shells around the Nucella lapillus shown above.
The hydrophone is based on a piezoelectric noisemaker, commonly found in things like home smoke detectors and Hannah Montana singing greeting cards (Note: it turns out that Hannah Montana greeting cards don't actually contain piezo discs. Stick with smoke detectors).
As sold,
these discs make a noise when you apply a voltage across the central
ceramic disc and the outer brass disc. But thanks to physics, you can do
exactly the opposite as well, produce a voltage across theceramic disc
and brass disc by making noise. The hydrophone exploits this property of
the piezoelectric noisemaker to turn it into a microphone.
I can
no longer find the paper that I read that originally described
thissetup, but someone at the Underwater Acoustics Group of the
Loughborough University of Technology put together this helpful pdf that
describes the construction of the same unit: Acheap
sensitive hydrophone for monitoring cetacean vocalisations.

The hydrophone
essentially consists of one of these piezo noise makers sandwiched between
two pieces of plexiglass, with an o-ring to providethe watertight seal
and make space for the wiring.
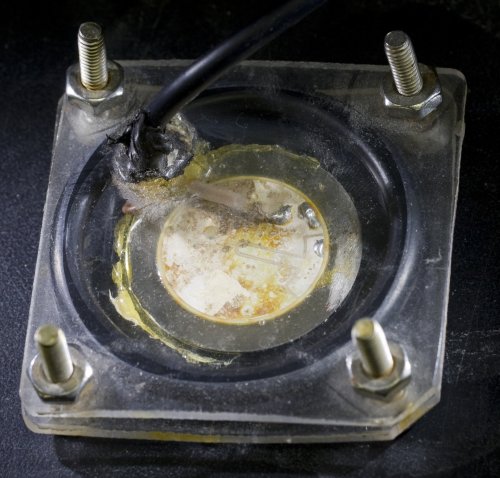
I used
a long mono headphone extension cord, as shown in the top picture,for my
wiring. The mono cord has two conductors in it. The central conductor
gets soldered to the ceramic central disc (visible in the picture above),
while the outer conductor gets soldered to the brass disc (not visible
above, but see the pdf for a diagram).
The wire
is passed through a drilled hole in one of the pieces of plexiglass,
which is sealed up with some sort of silicone caulk. 2-ton epoxy might be
good here as an alternative.
The other
side of the piezo disc then needs to be epoxied to the 2nd piece of
plexiglass. This provides a direct connection to the outside world
so that sound is transmitted efficiently from the water to the disc.
Spread some 2-ton epoxy between the disc and the plexiglass, and let it
cure.
The two
pieces of plexiglass then get sandwiched together with a thick o-ring
(something like McMaster-Carr part
number 2418T197) between them to keep water out. The bolts in each corner
need to be tight enough to slightly compress the o-ring. In my naive
youth I just went ahead and cranked things down until the plexiglass was
ready to snap, but it always worked fine.
Once everything
is put together, you should be able to just plug your cord into the
microphone input of a computer and start recording sound. It may be
necessary to crank up the amplification quite a bit due to the very low
level (low voltage) signal coming from the hydrophone.